A recent article in Packaging News prompted me to consider our role in the packaging industry as innovators and promoters of more efficient materials and processes. Rather than consider ourselves the victims of "wrap ragers" or "packaging bashers", we in the industry must be arbiters of change.
With thoughtful customers as our allies, we provide better packaging for increased product safety and durability, with less overall waste. One of our thoughtful customers is Analogic Corporation, of Peabody, MA - here is a story of their change to better packaging and the happy results:
While trying to meet the worldwide demands for their sensitive large scanners and imaging equipment, Analogic needed a packaging material that not only would give them the proper protection, but would also offer them an easy application that wouldn’t tie up their labor and slow down production.
Problem: Costly Returns, Service Calls and Packaging
The challenge was in shipping sophisticated equipment to many handlers around the world that may lack adequate warehousing, infrastructure, and handling equipment. As an OEM, Analogic sacrifices logistical control of their product once it leaves their facility. Customs inspections or the failure of ordinary packaging would leave their equipment exposed to severe and potentially damaging atmospheric conditions. This type of mishandling in the past resulted in costly freight returns from far off countries. Analogic looked into traditional barrier bags, but found them to be cost prohibitive because they take too long to put in place and vacuum out. Analogic also found that the time required to build the protective barrier created a bottleneck in the designate packaging area.
Solution: A Barrier Packaging Solution that Would
-
Give adequate protection for the toughest worldwide environments
-
Continue to work in these harsh environments even if there were punctures, slits and/or slices
-
Be quick and easy to put in place
-
Offer long-term, even years if necessary, protection.
Static Intercept™ “Quick Pack” Shrouds: Robust, Easy to Apply, Cost Effective
The Static Intercept "Quick Pack" Shroud system solved all of Analogic’s packaging problems. Without the need of heat-sealing or vacuuming, the Static Intercept 3 mil bottom sheet and 4 mil custom-built shroud can be applied in just seven minutes. With Static Intercept’s sacrificial means of corrosion protection, the material will continue to offer some protection, even if the barrier is punctured or torn. Analogic’s equipment would be safe from atmospheric attacks in shipment, as well as in storage, for long periods of time, and under varied environmental conditions.
Results: No Returns since Implementation
Since implementing the new packaging program using Static Intercept shrouds and bottom sheets, Analogic hasn’t had a single return due to corrosion in transit or in storage. In addition:
- Packaging workers are able to keep pace with production.
-
Production force now puts its efforts into building new items, instead of repairing damaged ones.
-
Management can have peace of mind that their equipment is safe when shipping to the harsh environments and storage conditions because Static Intercept provides that kind of assurance.
-
Production schedules don’t have to be built to keep the product fresh, because when stored in Static Intercept, the equipment will not degrade due to corrosion.
-
By utilizing the Intercept Technology to protect their fine equipment, Analogic maintains its reputation as a leader in the scanning and imaging field with customers that include several worldwide customers.
-
Analogic’s prestigious customers can be assured that "just off the line" type quality equipment can be provided each and every time.
-
All this is possible while improving their packaging protection.
Packaging as superhero? Read Packaging Saves the Day - Part One
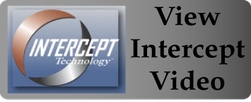
Intercept Technology Packaging products fit within a sustainability strategy because they are reusable, recyclable, do not contain or use volatile components (No VOCs, Not a VCI) and leave a smaller carbon footprint than most traditional protective packaging products.
Liberty Intercept Blog
Packaging Saves the Day - Part Two
Posted by Elaine Spitz on Nov 1, 2011 8:01:00 AM
With thoughtful customers as our allies, we provide better packaging for increased product safety and durability, with less overall waste. One of our thoughtful customers is Analogic Corporation, of Peabody, MA - here is a story of their change to better packaging and the happy results:
While trying to meet the worldwide demands for their sensitive large scanners and imaging equipment, Analogic needed a packaging material that not only would give them the proper protection, but would also offer them an easy application that wouldn’t tie up their labor and slow down production.
Problem: Costly Returns, Service Calls and Packaging
The challenge was in shipping sophisticated equipment to many handlers around the world that may lack adequate warehousing, infrastructure, and handling equipment. As an OEM, Analogic sacrifices logistical control of their product once it leaves their facility. Customs inspections or the failure of ordinary packaging would leave their equipment exposed to severe and potentially damaging atmospheric conditions. This type of mishandling in the past resulted in costly freight returns from far off countries. Analogic looked into traditional barrier bags, but found them to be cost prohibitive because they take too long to put in place and vacuum out. Analogic also found that the time required to build the protective barrier created a bottleneck in the designate packaging area.
Solution: A Barrier Packaging Solution that Would
Give adequate protection for the toughest worldwide environments
Continue to work in these harsh environments even if there were punctures, slits and/or slices
Be quick and easy to put in place
Offer long-term, even years if necessary, protection.
Static Intercept™ “Quick Pack” Shrouds: Robust, Easy to Apply, Cost Effective
The Static Intercept "Quick Pack" Shroud system solved all of Analogic’s packaging problems. Without the need of heat-sealing or vacuuming, the Static Intercept 3 mil bottom sheet and 4 mil custom-built shroud can be applied in just seven minutes. With Static Intercept’s sacrificial means of corrosion protection, the material will continue to offer some protection, even if the barrier is punctured or torn. Analogic’s equipment would be safe from atmospheric attacks in shipment, as well as in storage, for long periods of time, and under varied environmental conditions.
Results: No Returns since Implementation
Since implementing the new packaging program using Static Intercept shrouds and bottom sheets, Analogic hasn’t had a single return due to corrosion in transit or in storage. In addition:
Production force now puts its efforts into building new items, instead of repairing damaged ones.
Management can have peace of mind that their equipment is safe when shipping to the harsh environments and storage conditions because Static Intercept provides that kind of assurance.
Production schedules don’t have to be built to keep the product fresh, because when stored in Static Intercept, the equipment will not degrade due to corrosion.
By utilizing the Intercept Technology to protect their fine equipment, Analogic maintains its reputation as a leader in the scanning and imaging field with customers that include several worldwide customers.
Analogic’s prestigious customers can be assured that "just off the line" type quality equipment can be provided each and every time.
All this is possible while improving their packaging protection.
Packaging as superhero? Read Packaging Saves the Day - Part One
Intercept Technology Packaging products fit within a sustainability strategy because they are reusable, recyclable, do not contain or use volatile components (No VOCs, Not a VCI) and leave a smaller carbon footprint than most traditional protective packaging products.
Topics: anti-corrosion, barrier packaging, corrosion resistance, Static Intercept
Related Posts
Standard Corrosion Tests
Boston's Time Capsule - Contents Preserved with Copper: Part Two
Corrosion on Guitar Strings and How to Solve with Packaging
Leave a Comment